The Duty of Technology in Modern Welding Inspection Madison Practices
The Duty of Technology in Modern Welding Inspection Madison Practices
Blog Article
Exploring Advanced Tools and Approaches for Accurate Welding Examination
In the realm of welding inspection, the search of accuracy and reliability is extremely important, stimulating the advancement of cutting-edge devices and approaches. Technologies such as phased array ultrasonic screening and digital radiography are changing problem discovery, using unequaled precision in identifying welding flaws. Laser scanning developments and automatic examination systems, equipped with artificial intelligence, are redefining the landscape by minimizing human mistake and boosting safety and security measures. As these advanced techniques remain to progress, they assure not just to change assessment techniques yet likewise to increase interesting concerns about the future of quality control in industrial applications.
Ultrasonic Examining Developments
Ultrasonic screening technologies often represent the center of innovations in welding examination innovations. These developments have dramatically boosted the capacity to identify and examine stoppages within bonded structures, making sure improved honesty and safety - Welding Inspection Madison. Ultrasonic testing uses high-frequency acoustic waves to pass through products, giving detailed information about internal attributes without creating damage. The most recent growths in this area have actually concentrated on increasing accuracy, rate, and the ability to analyze complex information.
Additionally, innovations in software program algorithms for information evaluation have actually improved the accuracy of flaw discovery and sizing. Automated ultrasonic testing systems now use high-resolution imaging, enabling comprehensive assessments of weld quality. These systems are commonly incorporated with advanced visualization tools, which facilitate the interpretation of results.
Radiographic Evaluation Methods
While ultrasonic screening technologies have set a high standard in non-destructive examination, radiographic evaluation methods remain to play an integral role in welding assessment by supplying unique insights right into product integrity. Radiographic testing (RT) utilizes making use of X-rays or gamma rays to pass through materials, creating a radiograph that visually represents the interior structure of a weld. This imaging capability is vital for identifying subsurface issues such as porosity, incorporations, and splits that might not be noticeable with surface evaluations.
The process entails placing a radiation source on one side of the weld and a detector on the contrary side. Variants in material density and thickness impact the depletion of the rays, creating a contrasting photo that specifically defines defects. RT is particularly advantageous for evaluating thick areas and complex geometries where other methods might fail.
Regardless of its efficiency, radiographic assessment should be conducted with rigorous adherence to security protocols as a result of the harmful nature of ionizing radiation. Furthermore, the analysis of radiographs needs proficient workers, as the quality of the evaluation directly influences the integrity of the assessment. Ongoing developments in digital radiography are improving photo clarity and interpretation efficiency, strengthening RT's essential role in guaranteeing weld high quality.
Laser Scanning Breakthroughs
Accepting laser scanning innovation in welding assessment has transformed the assessment of weld top quality and honesty. Unlike standard evaluation techniques, laser scanning gives fast information purchase, considerably enhancing the performance and accuracy of weld evaluations.
Laser scanning breakthroughs have led to considerable improvements in characterizing and identifying surface area flaws such as porosity, absence of combination, and damages. The high-resolution data makes it possible for examiners to execute extensive evaluations, making sure that welds meet rigid industry standards. This technique sustains the growth of digital records, assisting in long-term quality assurance and traceability.
Furthermore, laser scanning modern technology integrates flawlessly with software services developed for automated issue discovery and analysis. The resultant information can be conveniently shared and reviewed, promoting collaborative decision-making processes. As markets continue to require greater criteria for weld top quality, laser scanning remains at the leading edge, supplying unequaled accuracy and efficiency in welding evaluation.
Automated Examination Systems
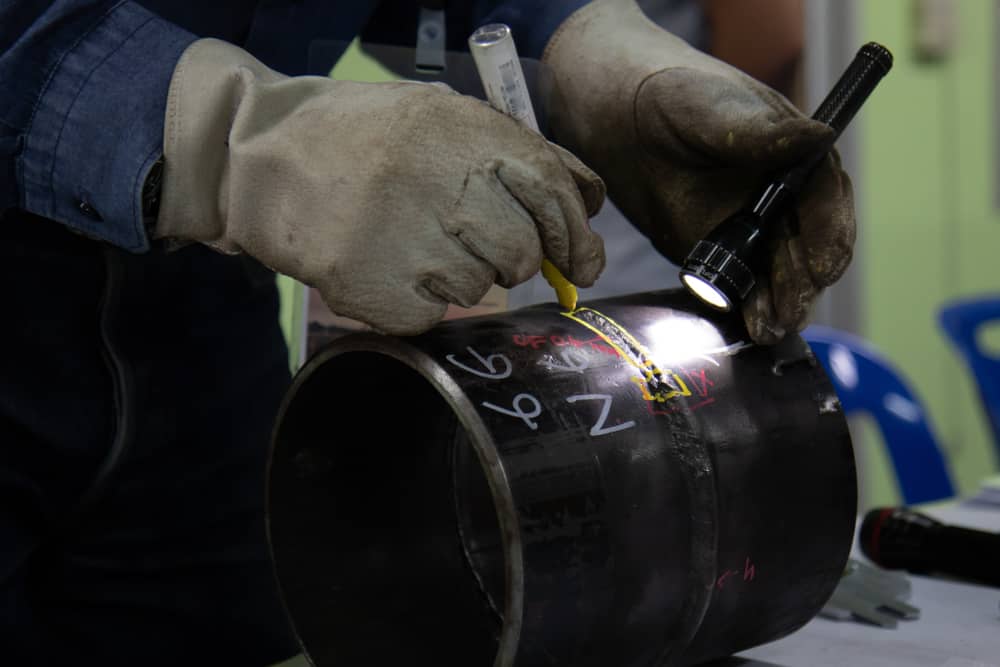
Automated examination systems provide the benefit of consistency, getting rid of human error and subjectivity from the This Site evaluation process. They are created to run in numerous environments, from manufacturing floors to remote field websites, guaranteeing extensive coverage. Welding Inspection Madison. These systems can be configured to abide by certain welding requirements and requirements, supplying in-depth records and documentation for quality control objectives
In addition, the integration of cloud-based systems promotes the storage and evaluation of large amounts of evaluation information. This makes it possible for pattern evaluation and predictive upkeep, enabling producers to resolve prospective problems before they escalate. The fostering of computerized assessment systems is an essential step in the direction of boosting the integrity and effectiveness of welding procedures in commercial applications.
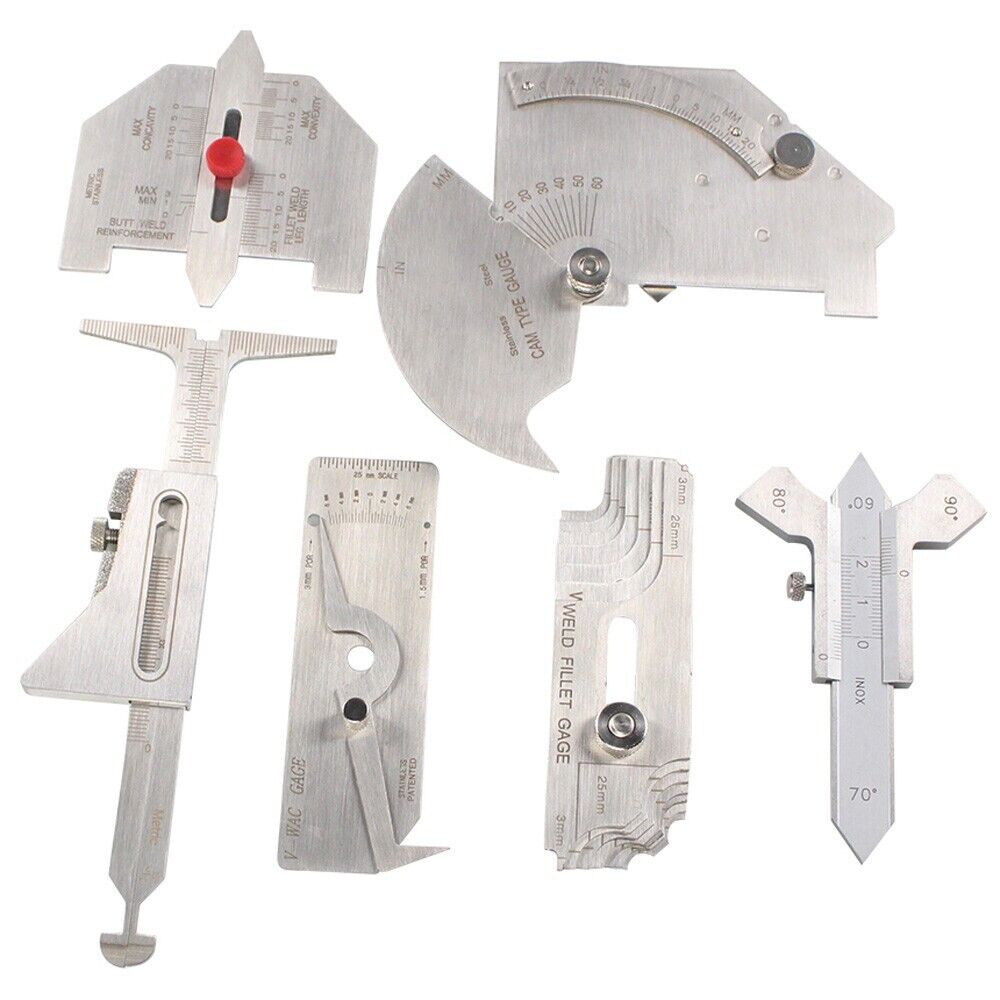
Enhancing Safety And Security and Efficiency
A considerable element of boosting safety and security and efficiency in welding evaluation hinges on the integration of cutting-edge innovations that streamline operations and minimize risks. The fostering of advanced non-destructive testing (NDT) techniques, such as ultrasonic screening, phased selection ultrasonic screening (PAUT), and radiographic testing, plays a crucial function in ensuring architectural stability without endangering the security of the personnel entailed. These methods enable comprehensive evaluations with minimal downtime, reducing prospective hazards related to standard techniques.
In addition, the execution of real-time data analytics and maker discovering formulas has actually changed the method examination data is interpreted. By employing anticipating analytics, prospective issues can be determined before they manifest into critical failings, making certain prompt interventions and upkeep. This positive strategy dramatically boosts functional performance and safety in welding processes.
Moreover, remote examination technologies, including drones and robotic spiders equipped with high-resolution electronic cameras, enable assessors to examine hard-to-reach locations without exposing additional hints them to harmful problems. This not just enhances assessment accuracy yet also lessens human danger. By leveraging these sophisticated devices and approaches, markets can attain greater safety and security criteria and functional efficiency, eventually causing more sustainable and trusted welding examination techniques.
Final Thought
The integration of advanced tools and techniques in welding evaluation substantially enhances problem detection and guarantees structural integrity. These improvements not just raise examination performance yet additionally add to improved security and quality assurance in commercial welding applications.

Ultrasonic screening advancements frequently stand for the center of innovations in welding assessment innovations.While ultrasonic testing innovations have actually established a high requirement in non-destructive assessment, radiographic assessment methods continue to play an important role in welding evaluation by using distinct understandings into product stability.Welcoming laser scanning innovation in welding inspection has actually revolutionized the analysis of weld high quality and honesty. As industries continue to demand greater standards for weld high quality, laser scanning remains at the center, providing unmatched precision and performance in welding evaluation.
Automated examination systems offer the benefit of uniformity, eliminating human mistake and subjectivity from the inspection process.
Report this page